Process Optimization
Process optimization plays a pivotal role in ensuring that companies can operate efficiently, maintain impeccable standards of quality in production or services, and consistently meet the expectations of their customers. Organizations can effectively allocate resources and concentrate on strategic initiatives that foster growth and enhance profitability by eliminating inefficiencies and streamlining processes.
Manufacturers can optimize manufacturing processes through a systematic approach to enhancing organizational efficiency. This is accomplished by improving various aspects of the manufacturing process. This practice shares common objectives with continual improvement, which aims to consistently improve processes, products, or services.
Process optimization encompasses a broad spectrum of improvements, including machinery enhancements, control adjustments, quality monitoring enhancements, and optimized maintenance scheduling. The overarching goal is to roll out processes that are significantly more efficient.
Steps for Successful Process Optimization
Process optimization is seldom a one-time endeavor. It is typically an ongoing process led by experts in operational excellence who adhere to systematic methodologies for planning, analyzing, and executing process enhancements.
When embarking on the journey of process optimization within an enterprise organization, several key steps should be followed:
The initial step involves clearly defining the objectives of the process optimization. This crucial phase helps establish the most effective approach for optimizing the process.
Following the objective definition, the current procedures should be thoroughly assessed to pinpoint areas where improvements can be made. This evaluation can be accomplished through techniques like process mapping or comprehensive data analysis.
Once areas for improvement have been identified, the next step is to craft an enhanced process that aligns with the optimization objectives. It’s essential to incorporate the requisite automation and technology to facilitate the optimization.
After developing the optimized process, it must be subject to rigorous testing to ascertain whether it aligns with the predefined optimization goals. This testing phase helps uncover potential issues or areas requiring further refinement.
With a validated process improvement, it’s time to introduce the optimized process throughout the organization. During this phase, ongoing monitoring and measurement may be necessary to ensure the optimization sustains the desired outcomes.
Process enhancements are rarely a one-time event. Many organizations engage in a continuous cycle of analyzing and refining core processes to achieve incremental improvements over time.
Industrial Process Optimization
Industrial plants can attain process optimization by following a systematic approach that encompasses the following key steps:
1. Identify Areas for Enhancement:
The initial phase involves identifying areas that require improvement. Optimization of industrial processes typically encompasses three main facets:
- Equipment Optimization: Ensuring that all tools operate at maximum efficiency.
- Operating Procedure Optimization: Standardizing procedures for optimal efficiency.
- Control Optimization: Ensuring that control loops managing processes are efficient and non-overlapping.
2. Access Real-time Data:
Modern technology provides numerous avenues for process optimization, with a common thread being the reliance on accurate, real-time plant data. Industrial Internet of Things (IIoT) devices play a pivotal role in monitoring all aspects of the plant and instantly sharing data, offering comprehensive visibility into plant operations.
3. Embrace Automation:
Automation is crucial in improving quality, consistency, compliance, and cost-effectiveness. By automating repetitive and time-consuming tasks, employees are liberated to focus on more intricate activities that contribute to process optimization.
4. Harness Artificial Intelligence (AI) and Machine Learning (ML):
AI and ML tools tailored to processes analyze real-time data to identify inefficiencies. They expedite root cause analysis, enabling swifter resolution of plant issues. Predictive analytics, a subset of AI, can detect early signs of emerging problems, facilitating preemptive corrective actions.
5. Monitor Progress:
Optimization of industrial processes is an ongoing endeavor, not a one-time task. Plant managers should establish Key Performance Indicators (KPIs) to measure the success of process optimization efforts and ensure that improvements remain on course.
By following these systematic steps, industrial and manufacturing plants can optimize manufacturing processes, enhance efficiency, reduce costs, and maintain operational excellence.
Process Optimization Techniques
Various methodologies and approaches exist to optimize manufacturing processes, each serving specific purposes. Varieties and techniques of process optimization include:
1. Process Mapping:
Process mapping involves visually documenting an entire process, from inception to conclusion. This method aids in pinpointing areas for improvement and streamlining the process.
2. Process Mining:
Process mining is a technique that employs data mining methods to discover, analyze, and enhance business processes. It expedites and automates the data collection phase of process analysis.
3. Root-Cause Analysis:
Root-cause analysis delves deeper into process analysis by examining the outcomes and identifying the underlying causes behind significant challenges and process issues.
4. Workflow Analysis:
Workflow analysis extends beyond individual processes or tasks to scrutinize and enhance end-to-end workflows, ensuring seamless operations.
5. Value Stream Mapping:
Value stream mapping, also referred to simply as time studies, involves creating a visual representation of the materials, data, or information pertinent to a project or initiative, aiding in optimizing value delivery.
These diverse approaches offer valuable tools for organizations to analyze, refine, and optimize their processes, thereby enhancing efficiency and effectiveness across various domains. Crow Engineering utilizes these optimization techniques as your one-stop for process optimization solutions, beginning with expert consultation through execution.
Benefits of Process Optimization
Optimization of processes holds significant importance for process manufacturing plants as it enables them to achieve several key benefits, including:
- Error Reduction: By implementing process optimization, manufacturing plants can significantly decrease the occurrence of errors, especially in tasks such as configuring processes and adding ingredients to mixtures.
- Enhanced Product Quality: Optimization of industrial processes contributes to an increase in the overall quality of products, ensuring that the final output meets or exceeds the desired standards.
- Minimized Downtime: Manufacturing plants can reduce equipment and plant downtime through effective optimization, thus maximizing operational efficiency.
- Time Savings: Optimizing manufacturing processes streamlines operations, reducing the time employees spend on tedious or repetitive tasks. This time can then be allocated to more valuable activities.
- Cost and Headcount Reduction: Optimization efforts lead to decreased production costs and staffing, resulting in improved profitability for manufacturing plants.
- Regulatory Compliance: Process optimization aids in achieving and maintaining compliance with both industrial and governmental regulations, ensuring that the plant operates within legal and safety parameters.
- Heightened Productivity: Overall, plant productivity receives a significant boost with the successful implementation of process optimization strategies.
Process optimization is the cornerstone of efficient and successful process manufacturing plants, offering a wide array of advantages that contribute to improved operations, product quality, and competitiveness within the industry.
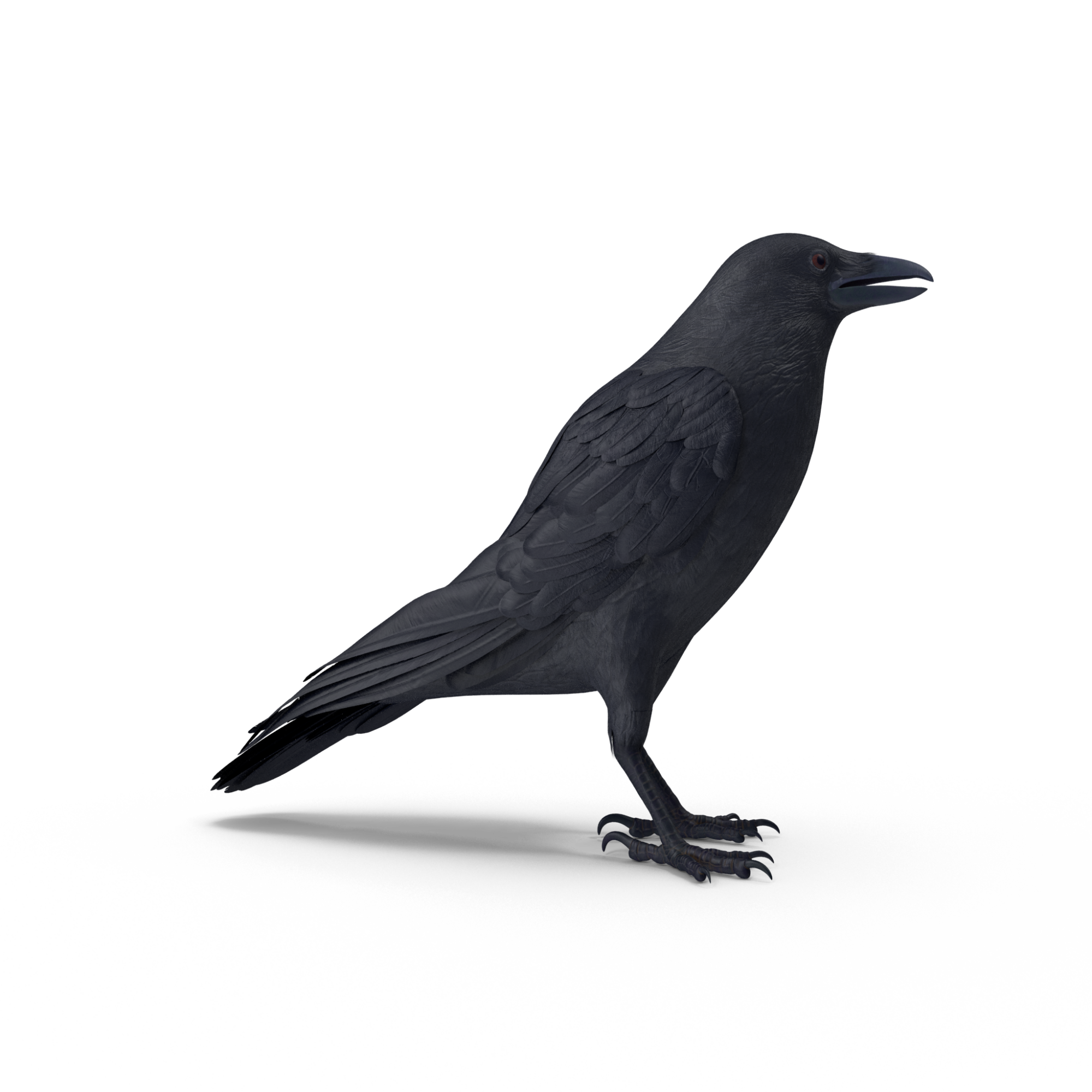
At Crow Engineering, we understand the complexities of industrial processes and what it takes to improve your overall business objectives. We are not just consultants; we are your partners in achieving operational excellence. With our process optimization services, you’ll have the expertise, support, and resources to optimize your manufacturing processes and stay ahead of the competition. Contact us today to unlock the full potential of your industrial processes and achieve operational excellence with proven strategies in process optimization.
the crow connection
Recent News
The Crow Connection delivers high-level insights on engineering, automation, and process optimization, helping you drive efficiency and innovation. Covering topics like AI-powered automation, manufacturing strategies, and industrial process improvements, it’s a must-read for leaders seeking a competitive edge.