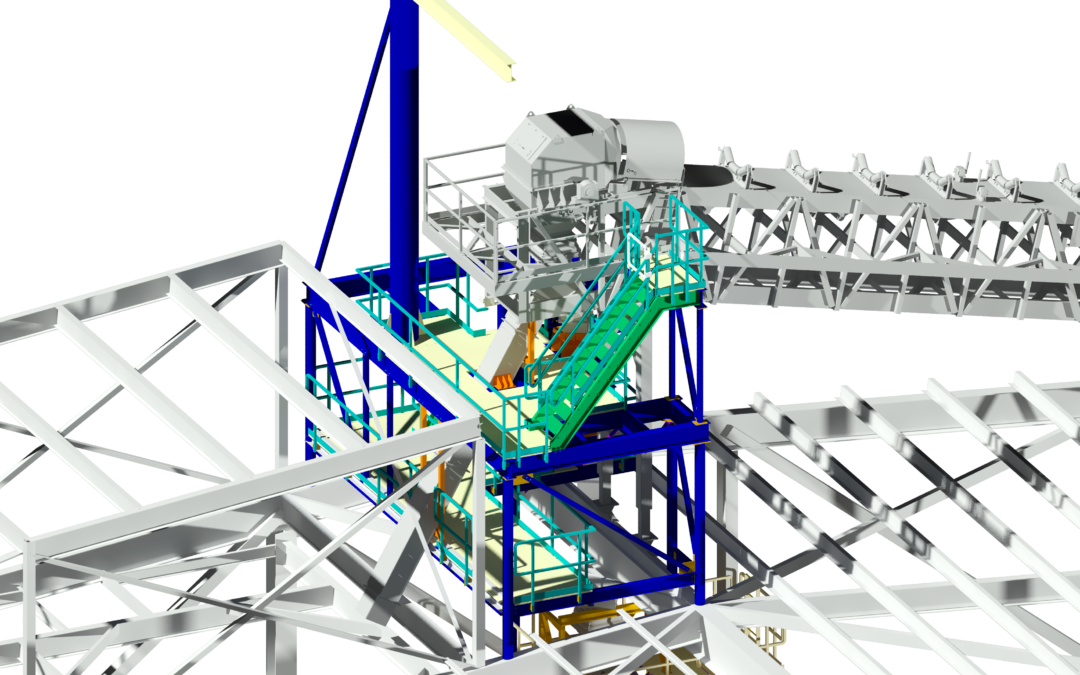
Modernizing a Mill with 3D
Recently, Crow Engineering completed an engineering design to replace a raw material infeed conveyor at a building products mill. The mill was connected to a mining operation with a single conveyor to deliver feedstock. The conveyor was built in 1962 and worn out. Any interruption or problems with this conveyor caused both mining and mill production to stop. The owner hired Crow to evaluate the situation and investigate possible solutions to replace, upgrade, or rebuild the raw material feed line.
The Crow team researched a variety of new and standard technologies and worked with multiple vendors representing their respective technologies. After evaluating and comparing possible solutions based on priorities, restrictions, and budget, the customer chose to build a new 450-foot long conveyor that rose to a height of 118 feet over existing buildings. Then a split flow would be engineered to separate three process lines via 100 foot long chutes that snaked around existing structures. Sounds simple, right? This project was anything but simple. However, Crow Engineering made this option viable by effectively using modern engineering tools.
Modern Tool No. 1 – 3D Scan
Two Crow engineers went onsite and conducted a 3D scan of the facility, verified the existing support structures, conditions of walkways, and verified missing as-built data not obtainable by the 3D scan. Crow presented the 3D scans and other field survey elements to the project participants. This 3D scan was used extensively with the conveyor vendor to avoid interferences and thread the chutes through a maze of structural steel.
Crow Engineering imported the vendor’s conveyor model into the 3D scan. Crow worked the project with real field data from the Crow offices and virtually walked thru the buildings identifying this door, this beam, this roof, and this path. These virtual reality meetings were more effective than being on-site. This saved travel time and Covid-19 issues were not a problem. A snapshot of design as shown below gives an example of what we could see:
Modern Tool No. 2 – Advance Steel 3D
Crow Engineering took the existing structural steel drawings and made a 3D model of the structure using Advance Steel (evaluated as the most cost-effective tool for this job). This model was then imported into the 3D scan so we could do a structural analysis and see where bracing had been modified or removed, where conduit and piping were added, how to route our conveyors and chutes, and ensured that we met current building codes.
Modern Tool No. 3 – SOLIDWORKS 3D
The conveyor vendor designs with SOLIDWORKS. The 3D model by the conveyor vendor was brought into Crow’s model of the structure. 3D snapshots were presented by Crow Engineering to the conveyor vendor showing where their conveyor and supports would hit existing obstructions. The conveyor vendor could easily see where the problems were and then modify their design. This went on for weeks with small modifications being made as their design progressed.
Modern Tool No. 4 – Microsoft Teams
Crow Engineering uses many modern-day collaborative tools. The conveyor vendor for this job is located in Mexico City, Crow is located in Beaverton, OR, and the owner’s team is located throughout the USA. Each week we would meet online and look at updated models and renderings to discuss ways to resolve issues. Crow believes that meeting weekly for one hour ensures that problems stay small, issues are resolved quickly, the project design flows smoother toward completion, and the “things to do” list stayed manageable. The modern way of doing business has become a new “norm” because of Covid-19 workarounds. Ultimately Crow Engineering and others have found that this method of collaboration has greatly improved project efficiency.
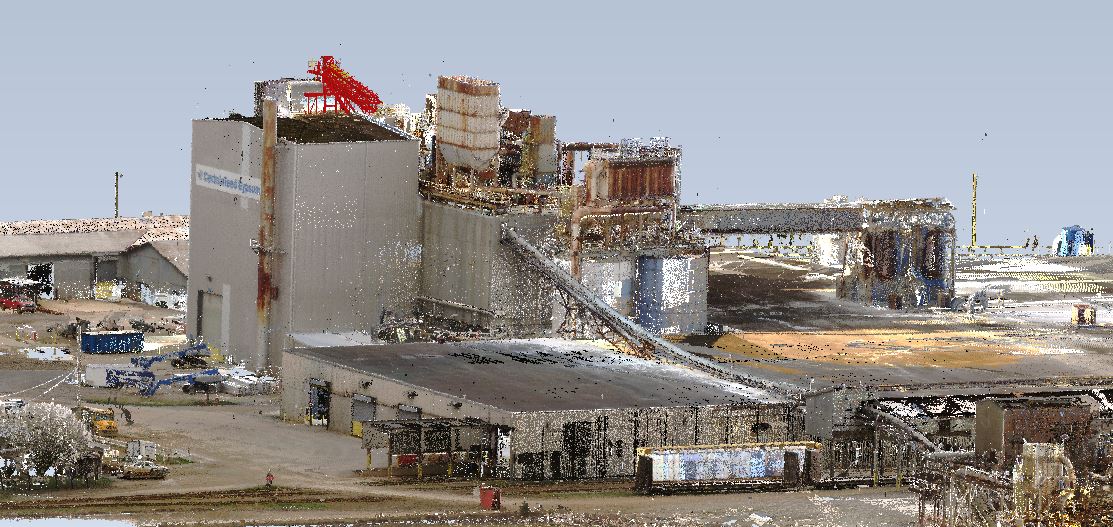
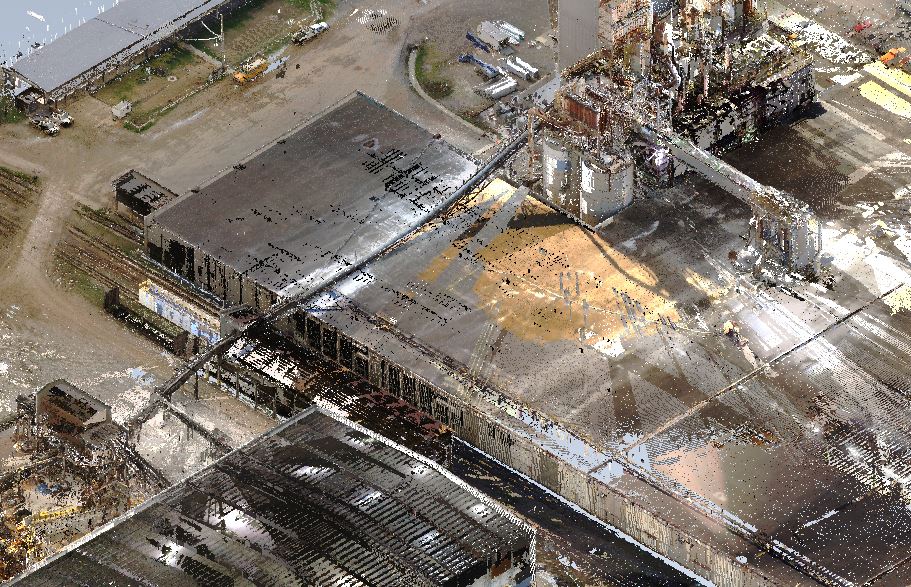
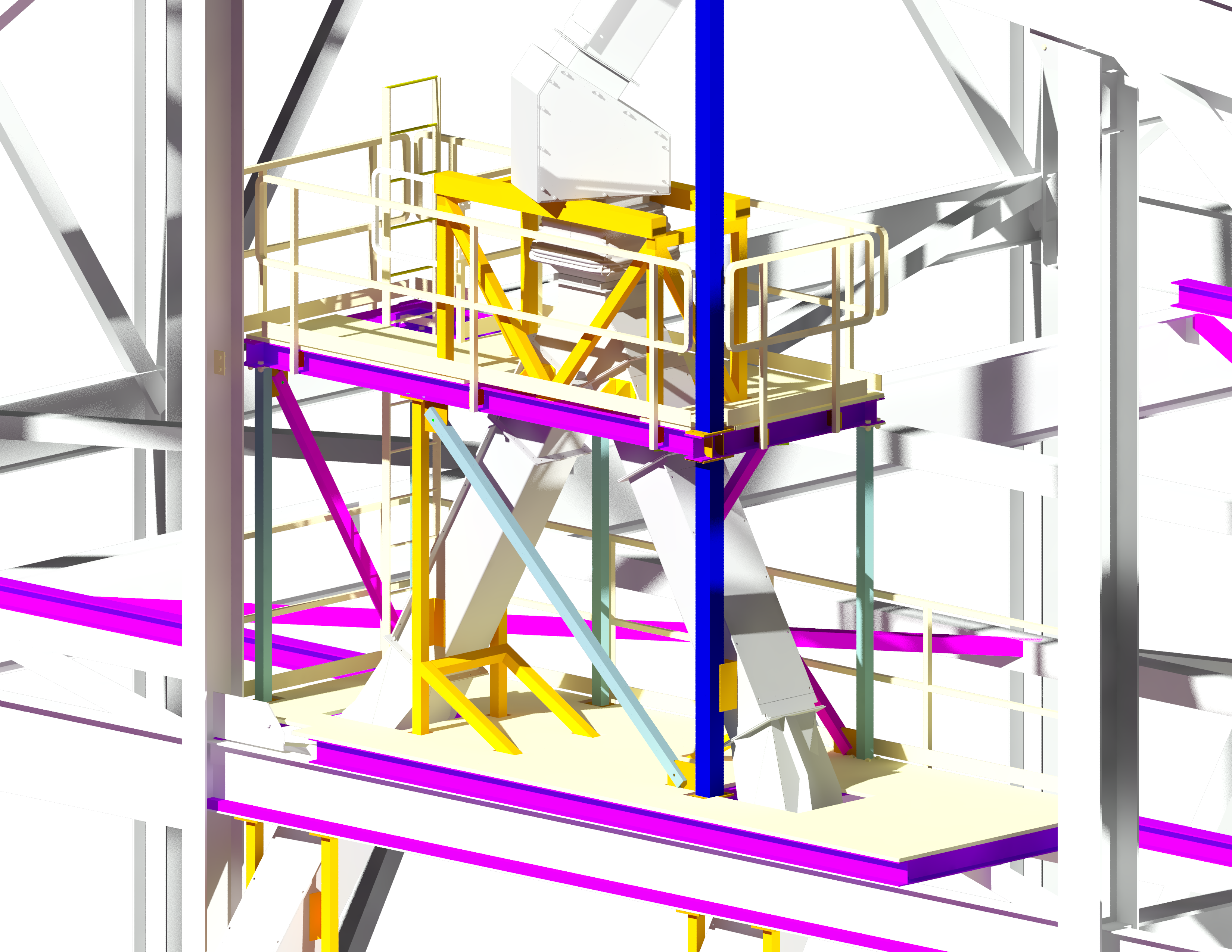
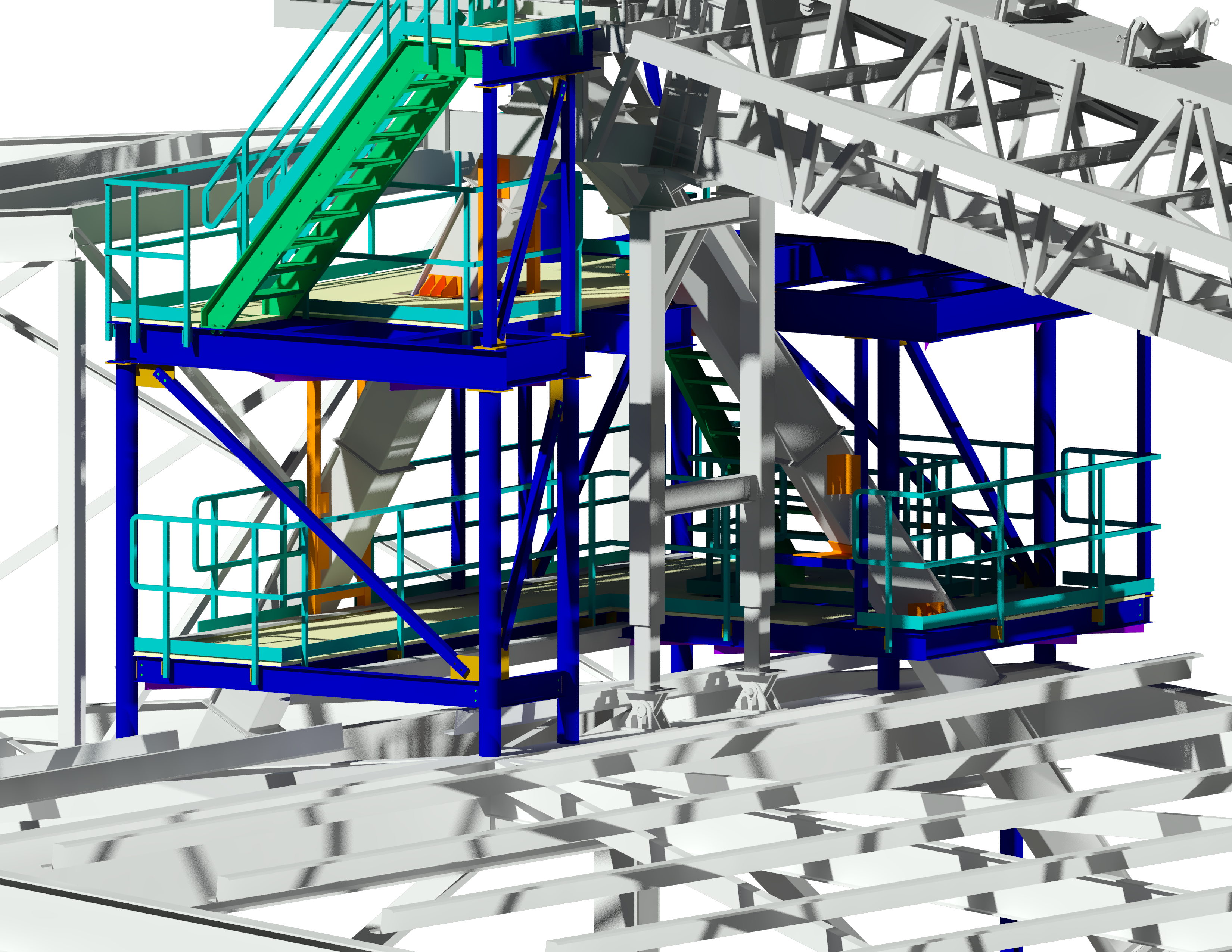
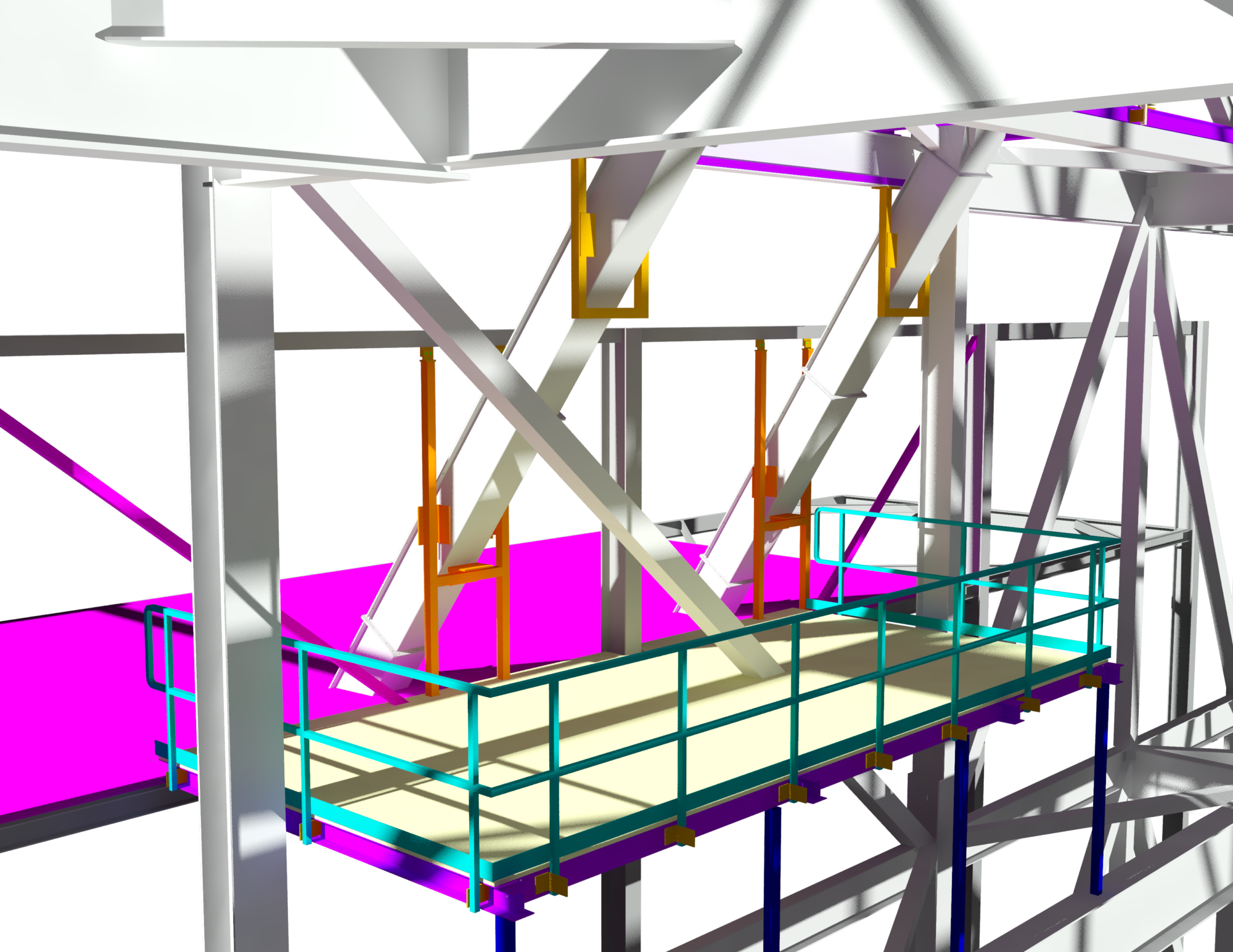
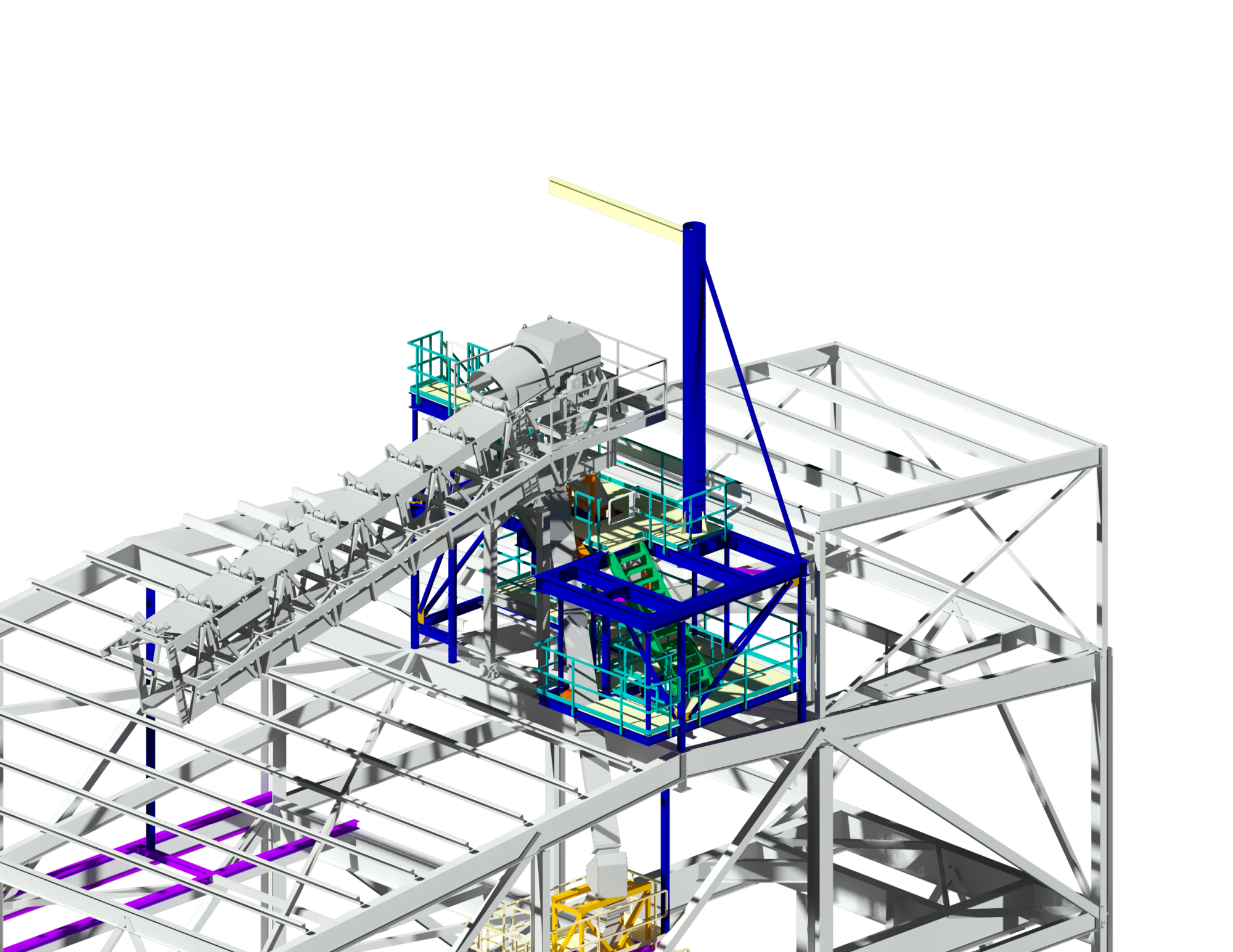
Keys to Success
Crow was involved in all phases of the project from consulting, engineering, and representing the client thru purchasing and execution. This guaranteed the design was delivered ready for construction and the project was on-time and on budget.
Crow Engineering provided all vendor and contractor bid packages and the bid evaluation system, designed per client priorities, to identify winning participants. Furthermore, Crow provided detailed design and shop drawings for parts of the project including building modifications, access, and supports for chutes.
We recognize the people below for their significant contribution to this project.
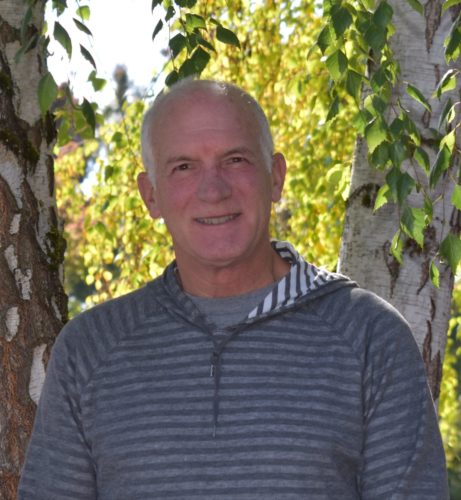
John Hansen
Project Manager
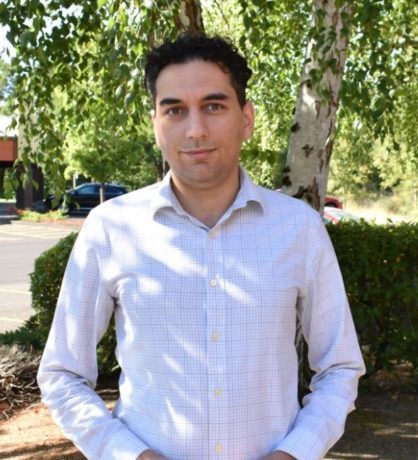
Mani Jenabzadeh
Mechanical Engineer
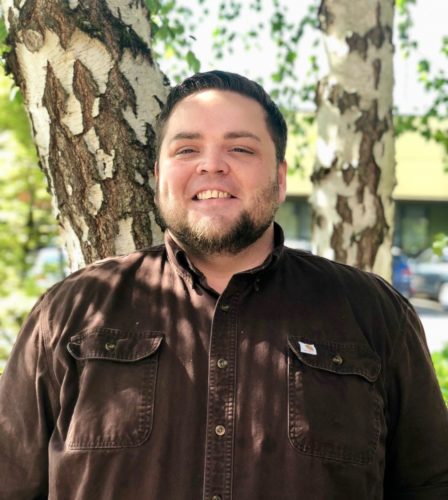
Chad Corkern
Structural Engineer
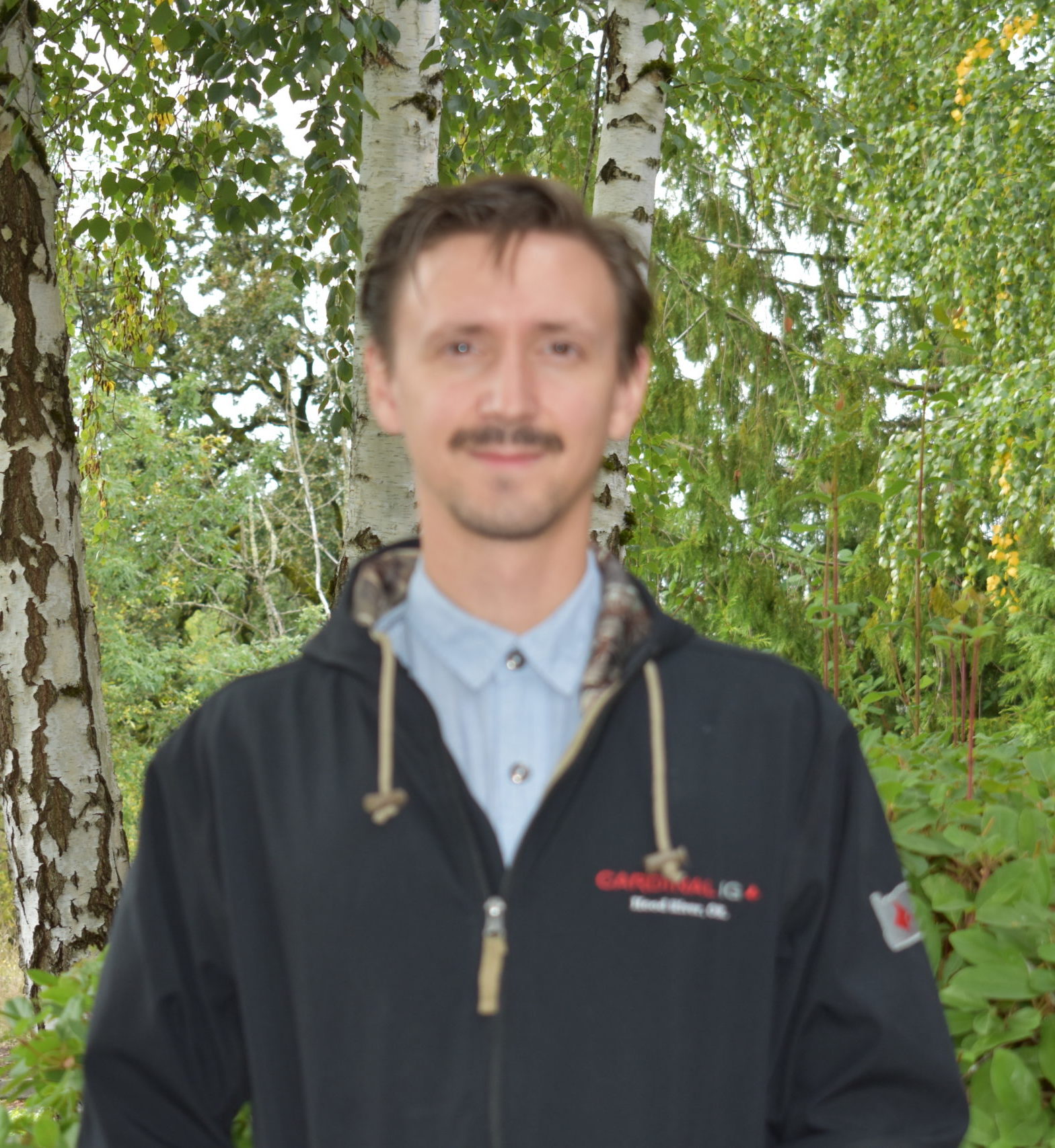
Trevor Stobbe
Designer