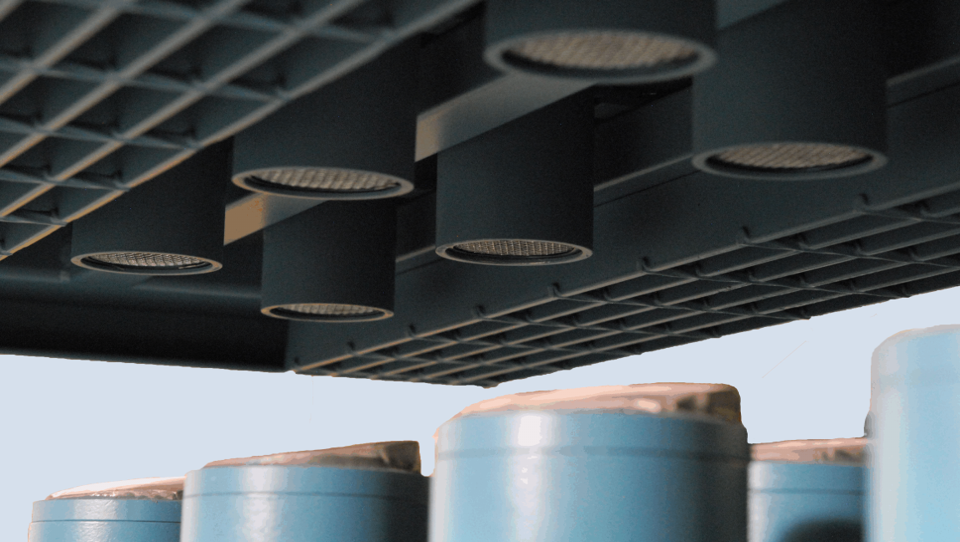
AIC Systems Still Up and Running After 30 Years
In 1973, Automation Industries Corporation (AIC, now Miloptic) developed blow detectors that used air-coupled ultrasonic nondestructive testing technology. Now, several of the systems – installed more than 30 years ago at panel and flooring facilities – are still up and running. These systems help manufacturers improve the quality of their products by:
- Assuring internal bond quality at full process rates after the press, saws, or sander
- Optimizing the recovery of good material from master panels containing defects
- Optimizing pressing recipes
- Eliminating delamination claims from the field
- Reducing defectives and downgrades by early detection of process problems
Why are these systems still functioning and delivering value?
Mainly because they were carefully developed with embedded PCs to avoid obsolescence risk and with innovative technology to ensure immunity to the airborne interference sources.
Sophisticated acoustic filters eliminate potential plant-ambient interference, resulting in high signal-to-noise ratios and accurate, reliable performance. Also, the Miloptic systems do not use ceramic crystal-based transducers to avoid sensitivity drift and inefficient coupling into air. Many air coupled ceramic devices were designed for use in burglar alarms and rudimentary piece counting applications, all of which do not have stringent requirements associated with nondestructively testing wood fiber-based products in a full industrial manufacturing environment. Transducers using ceramic piezoelectric crystals are sensitive to temperature variation, causing good panels to be identified as defective. Miloptic transducers are, at a minimum, five times as efficient at coupling ultrasound into and out of air when compared to ceramic crystal.
The quality and toughness of the steel scanner frame included design details such as easy access to transmitters and receivers. When transducers need to be replaced, the technician can remove them in less than one minute, making cleaning easy and efficient. The transmitter covers can be removed in seconds should they become damaged. During startup, mounting buckets are locked in place to ensure transducers are not later misaligned.
Almost fifty years and still going strong! Miloptic is committed to the ongoing development and production of durable, high-quality systems to serve the needs of the wood product industry for decades to come.
“Crow’s goal is to continue to be the first place mills turn to for help with improving their operations. Traditionally this support has come from capital and maintenance project support. This acquisition, and the recent addition of PLC and electrical capabilities now allows us to help our clients in optimizing their operations. We are excited to have this opportunity with the AIC team and the 40+ years of experience they bring to the table!”
Hunter Wylie
Crow Engineering’s President